Business Case: Cooling Tower
Negative environmental influences and effects on health, especially due to legionella, must be minimized by appropriate measures.
Specialist companies offer a wide range of customized treatment concepts based on conditioning chemicals that prevent corrosion, inorganic deposits and microbiological growth.
The active ingredients used, which have to be dosed according to the respective processes, should:
- enable optimum heat transfer
- prevent blockage of pipes, fittings and pumps
- prevent system failures and operational malfunctions
- reduce operating costs and maintenance efforts
Continuous monitoring of important and particularly critical water parameters is mandatory to control the effect of the products used and to evaluate the condition of the cooling system in the long term.
Initial situation / As-is analysis
Evaporative cooling systems, cooling towers and wet separators can, under certain conditions, release aerosols (very fine water droplets) containing legionella into the outside air, which can lead to severe pneumonia and consequently even death if inhaled.Legionella are bacteria found in natural waters and soils. Normally, they do not pose a health hazard in this context.
Figure 1: Rentokil THS
In recent years, such Legionella outbreaks with fatalities have occurred repeatedly in Germany, for example in Warstein in 2013 and in Ulm/Neu-Ulm in 2010.
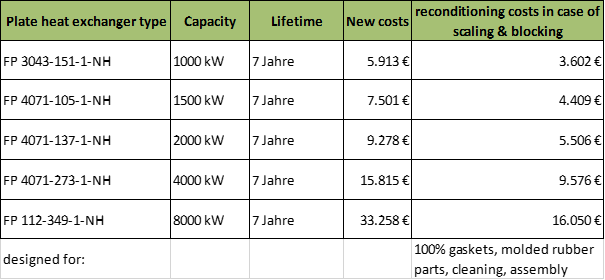
The 42nd Ordinance to the Federal Immission Control Act (42. BImSchV) on Evaporative Cooling Plants, Cooling Towers and Wet Separators regulates the essential requirements for the construction, operation and monitoring of the more than 30,000 plants in Germany. The ordinance summarizes the most important obligations for plant operators of evaporative cooling plants and wet separators.
Since water is the natural medium for the cooling tower, it also poses challenges in terms of proper and safe operation. The two most important factors here are water hardness and biological loads. The composition of the water is always site-specific and is significantly influenced by the source of the water used and the site-specific factors prevailing there. High concentrations of calcium and magnesium, the so-called hardness components in the water, lead to lime deposits in the water due to its circulation through a heat exchanger. These inevitably lead to a loss of performance of the heat exchanger and result in higher energy costs. In the worst case, there is even a risk of production downtime.
Even a limescale layer of only 1 mm reduces the performance of the cooling tower by approx. 30 percent. As a result of these deposits, the cooling tower has to be operated at higher fan speeds, energy consumption increases and the system capacity can be described as limited.
Another danger of lime deposits in the system is the trapped corrosion spots. If a corroded area is "closed" or covered by a lime deposit, the corrosion spreads under this "protective layer" and major damage is inevitably caused. For the above reason, a so-called corrosion inhibitor is added to the water. The inhibitor forms a protective layer on the inside of the pipe and prevents, among other things, the deposition of the hardening agents on the inner wall of the pipe.
Depending on the size of the system, damage can quickly result in high costs. In addition to the pipelines and valves, the heat exchangers should be mentioned here, the costs of which can be represented as follows:
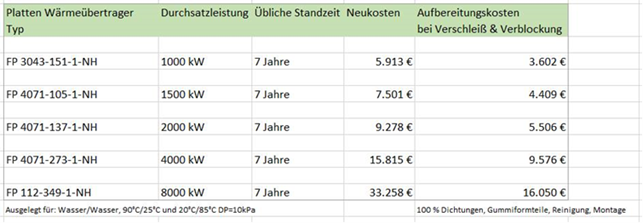
Source: Funke Wärmeaustauscher Apparatebau GmbH; Status 12/2021
Based on the quality of the make-up water used, various processes or combinations thereof have proven effective for technical operation. These include, for example, the use of softening plants to reduce the water hardness of the feed water. In combination with chemical products such as hardness stabilizers, deposits can be effectively avoided and costs saved.
The increasing relevance of cooling processes in industry, coupled with a global decline in the natural resource of water, is presenting operators and planners with ever new challenges in terms of the reliable availability of make-up water. Increasingly, not only a supply source such as the local supply network, but also locally accessible sources such as surface waters or groundwater are being used to ensure safe and economical operation of the plants.
In addition to the challenges already mentioned with regard to the provision of the necessary volumes in the required water quality, the operation of a cooling system is also subject to external influences, which consequently cause an input of biological mass including bacteria, etc. If these are not counteracted, the cooling system can be damaged.
If these are not counteracted, biological deposits occur in the systems, which are also colloquially referred to as biofilm. The biofilm thus represents a contamination of the circuit and is the source and growth site for a wide variety of microorganisms, such as Legionella. In modern water treatment, a wide variety of disinfection media are available that prevent the growth of biofilm. A particular challenge in the use of these products is to ensure permanent disinfection. This is a technologically demanding process, especially in view of the adaptability of the microorganisms and the specific effect of the disinfection medium, and requires highly accurate monitoring. If this process is not monitored and checked for the specific conditions, the biofilm may continue to grow and, at a later stage, the microorganisms contained may be detached and discharged via the aerosols.
The exact costs for the conditioning process depend primarily on the available water quality, type and number of feed sources and require extensive water analysis in advance of the technical design and selection of the products to be used. The following costs for equipment and chemical treatment can be assumed as a rough guide.
Type of Construction |
Output |
Water treatment costs* |
Costs measuring, metering & monitoring technology |
Compact reccoling units ![]() |
up to 2.000 KW |
Ca. 5.000€/year |
up to 7.500€ |
Cellular cooling tower ![]() |
7.500 – 10.000€ |
up to 10.000€ |
|
Natural draft wet cooling tower ![]() |
> 200 MW |
80.000 – 120.000€/year |
size-dependent or throughput-dependent from 17.500 € |
* Costs are significantly influenced by the type of make-up water and the microbiological condition
All these measures serve to protect the population from legionella outbreaks, have a direct connection to the economic operation of the entire plant and the conservation of natural resources. In summary, it can be said that in addition to the liability risks involved in non-compliance with the legal requirements, monetary aspects such as the protection of natural resources, energy savings and the reduction of costs for the chemicals used, a comprehensive consideration of this complex topic is not only desirable but mandatory for all groups of people involved.
The key players within this process are:
- Management of the operating site: fundamental responsibility for proper operation, taking into account legal requirements; review of current recommendations for action.
- Technical Operations Management: Responsible for: Checking the plant for proper operation; maintaining and archiving records that require documentation.
- Conditioning chemical manufacturer: responsible for: proper dosing to ensure legally compliant operation of the plant, considering current and ongoing water analysis; providing appropriate technology to meet legal requirements, protecting water-bearing systems from deposits & damage.
Investigated solution variants
In summary, it must be stated that cooling towers are complex technical systems which are naturally subject to various influencing factors and do not represent a statically self-contained system. This makes the monitoring of operational and environmental parameters and operating conditions all the more important.In the following example, a process is shown which includes some of the measuring methods usually used. The combination of the methods and monitoring functions shown always depends on the chemical conditioning methods used, the structural conditions, including the materials used, and the general operating conditions, such as the water composition.
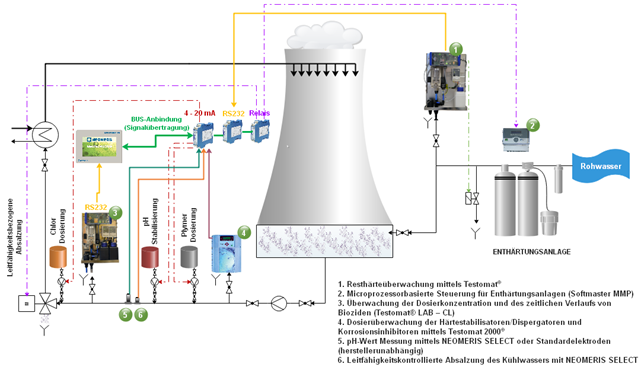
The following components can be seen in the example of cooling water monitoring shown:
- Residual hardness monitoring via Testomat LAB TH®
The monitoring of the softened make-up water ensures that the upstream softening plant is working properly. In the event of a limit value being exceeded (freely programmable), this is transferred as information to the NeoTecMaster®, an open-manufacturer multicontroller, which as a result transfers the start signal for regeneration to the Softmaster MMP via a potential-free contact.
- Microprocessor-based control for softening plants (Softmaster MMP)
The quality-controlled triggering of the regeneration of a softening plant represents the most accurate and at the same time most environmentally friendly process. By integrating the Testomat® into the control and monitoring concept, regeneration is only triggered in case of actual demand. In addition to saving operating costs for salt and wastewater, this process has the advantage that regeneration is also reliably triggered in the event of fluctuations in the input water hardness and thus the composition of the circuit water is continuously available in a known quantity with regard to the hardness components calcium and magnesium, which in turn enables the use of so-called hardness stabilizers to be optimized.
- Monitoring of the dosing concentration and the time course of biocides (Testomat® LAB CL)
Chemical conditioning of the circulating water is required to ensure compliance with the legal requirements and the associated hygiene requirements in accordance with VDI 2047 Sheet 2 and the 42nd BImSchV. In particular, the issue of germination and the formation of biofilms must be taken into account. The use of biocides essentially serves this purpose:- The prevention of biofilms in e.g. heat exchangers and thus the prevention of a reduction in efficiency (biofilms act as an insulating layer).
- To protect the material surfaces in contact with the water from corrosion by acid-forming bacteria.
- The discharge of microorganisms such as Legionella via aerosols.
In practice, a wide variety of biocidal products are available for this purpose. The most common are biocides based on chlorine, chlorine dioxide and combination products of hydrogen peroxide and silver.
In practice, a wide variety of biocidal products are available for this purpose. The most common are biocides based on chlorine, chlorine dioxide and combination products of hydrogen peroxide and silver.
The Testomat® LAB CL (DPD method) allows the monitoring of the concentration in the circuit water when using a biocide containing chlorine. The measurement results can be transferred directly to a higher-level control system by means of a 4-20 mA signal or RS232. On the software side, the NeoTecMaster® has several functions for processing the actual signal and thus allows dosing as required by means of a standard or invert signal. - Dosing monitoring of the hardness stabilizers/dispersants and corrosion inhibitors via Testomat 2000®
A further focus of the necessary chemical conditioning of the circuit water is the protection of the entire system against deposits and calcification. For this purpose, hardness stabilizers are used selectively to prevent or significantly reduce the precipitation of calcium carbonate. Dispersants are used to prevent various deposits, such as various suspended solids based on dirt, iron oxides, manganese oxides, etc., from forming. are used. Dispersants keep solids "in suspension", which can therefore not or only slightly deposit in the system. Corrosion inhibitors are often based on molybdate, polyphosphates, zinc, phosphonates, toluyl triazole or sodium hydroxide. The corrosion protection is achieved by:- the formation of a protective layer on materials
- a significant reduction of the electrochemical corrosion process and
- if necessary, alkalization (raising of the pH value)
The analysis of active ingredients based on special polymers, phosphonates and polyphosphates, is possible using Testomat® 2000 Polymer or Testomat® 2000 o-PO4. The results of the online measurement are transferred by means of a 4-20 mA signal either directly to a dosing pump or beforehand to a central control system.
- pH value measurement using NeoTec Select or standard electrodes (independent of manufacturer)
The pH value indicates how acidic or basic a water is. Water with a pH value around 7 is called neutral. Depending on the materials used, the pH value of the cooling water should be in a range of 7.0 - 8.5. The monitoring of this parameter is particularly relevant when supplementary water is introduced, as the carbonic acid is expelled via the cooling tower and the pH value increases as a result. As a result, the natural "lime-carbonic acid balance" is disturbed and the tendency to deposit increases significantly.
NeoTec Select has special flat-head electrodes available for monitoring the pH value, which are particularly suitable for use in the cooling tower area due to their technical design and the sensor head geometry. The flat design of the electrode head minimizes deposits on the sensitive sensor surface. The integrated 4-20mA head transmitter enables transmission to the NeoTecMaster® system or, if required, direct control of the associated dosing technology.
The monitoring of the pH-value, in connection with a corresponding pH-value stabilization, minimizes the use of conditioning products and at the same time allows an increase of the thickening rates. As a result, the environment is protected and costs on the wastewater side are reduced.
Figure 2: Flat head electrode NeoTec Select
Figure 3: View of Ring-Diaphragm
Conductivity-controlled desalination of the cooling water with NeoTec Select
One of the most important parameters for the monitoring of a cooling circuit is the conductivity. Conductivity is a measure of the number of dissolved salts and thus allows conclusions to be drawn about the condition of the water. Too high conductivity promotes corrosion, among other things.
Cooling towers are based on the principle of evaporation, which means that this ensures the cooling capacity. Roughly, a cooling capacity of 650kW is assumed per cubic meter of evaporated water.
Since only the pure water (H2O) evaporates, the substances contained in the water are concentrated. This process is also called "thickening". Thickening is the ratio of the salt concentration of the cooling circuit to that of the make-up water. Against this background, conductivity has become established in practice for monitoring, since as a sum parameter it has a very high informative value regarding "thickening" of the circulating water.
Without technical intervention, the salt concentration in the circulating water would increase uncontrollably and lead to deposits in the system after reaching the solubility limit. As a further negative effect of thickening, it should be mentioned that such salt-enriched waters are ideal breeding grounds for algae and bacteria, which find optimal conditions for biological growth at the temperatures of approx. 25 to 35 °C usually present.
For the above reasons, the so-called conductivity-related desalination is carried out with knowledge of the overall process. Practice has shown that a maximum thickening by a factor of 4 is useful for this purpose. Higher thickening numbers very rarely have a corresponding increased monetary effect on the operating costs. For this purpose, a maximum permissible conductivity is defined for the blowdown, considering all influencing factors as well as the chemical conditioning products used. When this threshold value is reached, all dosing processes are blocked and the now concentrated water is drained off in a controlled manner via a blowdown valve and replaced by fresh filling water. The desalination process is then interrupted so that the conditioning products added to the water again can take effect.
The conductivity measurement can be carried out either with a NeoTec Select probe or with a standard product from other manufacturers.
This exemplary measurement and control concept is based on the metrological requirements of cooling tower operators. Continuous monitoring of the measurement parameters and the water quality is an important prerequisite for reliable and economical plant operation.
We would like to thank the following companies for their support in the collection of business data as well as their technical support:
- Funke Wärmeaustauscher Apparatebau GmbH: FUNKE Wärmeaustauscher - Funke Wärmeaústauscher
und
- CG Chemikaliengesellschaft mit beschränkter Haftung & Co. KG: CG 1962 | Chemikalien | Chemie die verbindet | CG 1962 (cg-chemikalien.de)
In addition to achieving maximum process reliability, the primary objective in monitoring the cooling tower process should always be the responsible use of water as a natural resource and the use of biocides to ensure a sustainable approach to the environment.